The Test of Strength: Forged vs. Cast
Forged steel pistons and cast steel pistons look similar but have vast differences in their manufacturing processes which affect their durability and performance.
Forged steel pistons are made through thermal and mechanical energy delivered with a hammer to steel billets causing the material to change shape while in a solid state. When questioning durability, forged steel is generally stronger and more reliable than cast steel because the grain flows of the steel are altered during the tooling process, conforming to the shape of the part (as pictured below). This creates uniformity of composition and structure resulting in metallurgical recrystallization and grain refinement because of the thermal cycle and deformation process. As a result, the finished steel product is stronger.
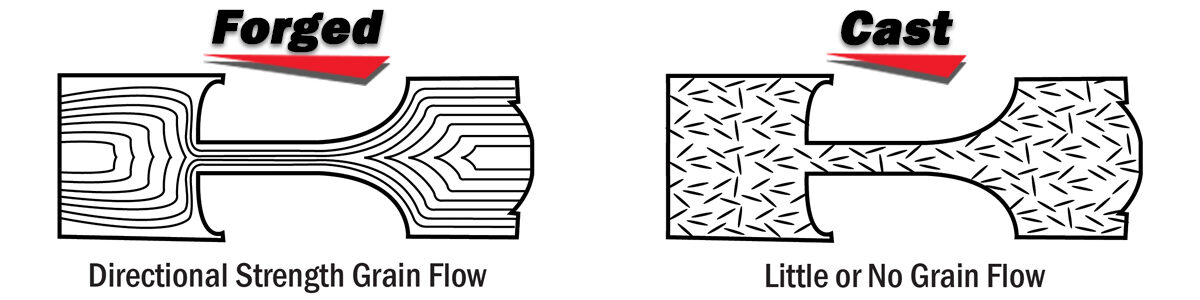
For the creation of cast steel, the steel is heated until it reaches a molten state and then it is poured into a mold to create a desired shape. Casting cannot obtain the strengthening characteristics of forged steel due to the single step process of a molten pour. A casting has neither grain flow nor directional strength and the process does not prevent formation of certain metallurgical defects. These defects occur in a variety of forms from impurities being trapped below the surface to vapor bubble and micro fractures.
Interstate-McBee has developed strong relationships with the top manufacturers in the world to produce the forged steel pistons in our product lines. As more engine models are developed using the strength and durability benefits of forged steel pistons our product line will continue to expand.
Below is a full listing of our engine applications that feature forged steel pistons.
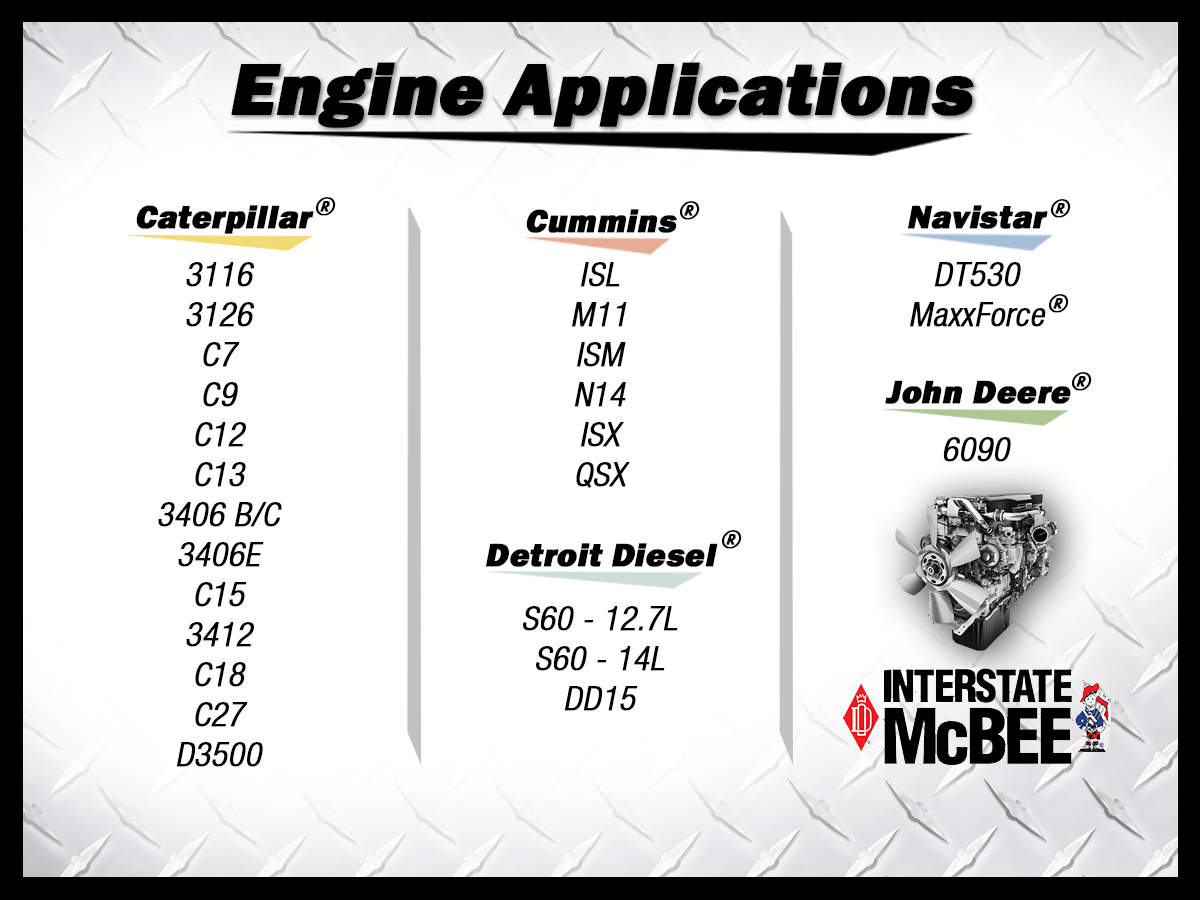